An Overview of Sheet Metal Stamping Presses
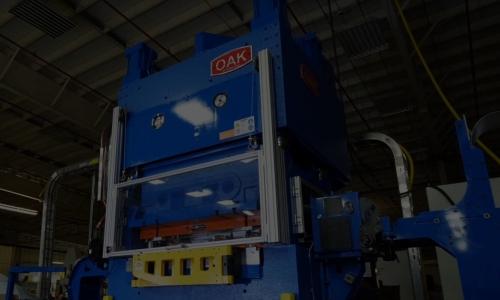
In general, sheet metal stamping is a kind of cold forming process where intense force and/or speed is used to permanently change the shape of sheet metal. This process of altering metal is also referred to as pressing because of the use of the press to accomplish the task. Simple to understand, sheet metal stamping involves large amounts of tool and die that is put into a press that exerts high amount of force in very little time to press sheet metal into the exact shape you need for your project.
The Main Functions of a Sheet Metal Stamping Press
Flattening Metal. Flattening metal is one of the most common and basic operations of a stamping press and is used to either make the metal more smooth or more thin.
Piercing Metal. Just as it sounds, sheet metal stamping presses are also used to pierce metal, puncturing it all the way through in order to create openings that are then typically used to connect other pieces of metal.
Coining Metal. If you are in need a shape other than just a small hole, the press can be used to press the sheet metal into a specific shape, like a coin.
Swaging Rounded Metal. Also a way to flatten metal, this process is typical used to make wires more thin so that they can more easily fit into an opening.
At OAK Press Solutions, we manufacture 30 to 300 ton mechanical presses for the general sheet metal stamping industry, with the capability of setting up turnkey systems for our customers. We will do as much or as little as you want, if you just want a press and a feed we will accommodate that, or we can help design your complete line from beginning to end with; uncoiler, material loop control, feed, die, anything that can go in a press line. We set up the system in house and do not ship it until our customer signs off on the factory runoff.